Homelander The Seven
I will laser every f****** one of you!
Ngày 10/7/2025, trong buổi họp chiến lược trực tuyến dành cho nhà đầu tư, Phó Chủ tịch Điều hành Toshio Nakanishi của DNP đã công bố khoản đầu tư 300 tỷ yên cho mặt hàng photomask trong 3 năm tới (2026-2028). Theo Nikkei Asia, con số này tăng 50% so với giai đoạn kinh doanh trung hạn trước (2023-2025), thể hiện tham vọng mở rộng quy mô sản xuất. Mục tiêu DNP là tăng doanh thu photomask lên 55% vào năm 2028, đáp ứng nhu cầu đa dạng từ chip cao cấp (như chip 2nm cho AI) đến chip trung cấp và phổ thông (cho thiết bị tiêu dùng).
Photomask là “bản gốc” để in mạch lên wafer silicon, đóng vai trò then chốt trong sản xuất bán dẫn. DNP dự định tập trung vào hai hướng: sản xuất hàng loạt photomask EUV từ năm 2027 và tăng cường sản xuất photomask truyền thống cho các phân khúc khác. EUV là công nghệ tiên tiến, cần thiết để tạo ra các chip siêu nhỏ (2nm, 3nm) cho smartphone, trung tâm dữ liệu và AI. Theo EE Times Japan, DNP đã đạt thành tựu lớn khi thử nghiệm thành công mẫu mạch 2nm vào tháng 12/2024, đặt nền móng cho việc hợp tác với công ty Nhật Bản Rapidus, nhắm đến sản xuất chip 2nm vào 2027.
So sánh với đối thủ, DNP đang cạnh tranh khốc liệt với Toppan Photomasks, một công ty Nhật Bản khác. Theo Semiconductor Digest, Toppan hiện chiếm khoảng 15% thị phần photomask toàn cầu, trong khi DNP chiếm 10%. Tuy nhiên, khoản đầu tư 300 tỷ yên và hợp tác với Rapidus có thể giúp DNP vượt lên, đặc biệt ở phân khúc EUV.
Một điểm sáng trong kế hoạch DNP là phát triển Nanoimprint Lithography (NIL), công nghệ in nano được xem là giải pháp thay thế cho EUV. Theo Nikkei Asia, DNP sẽ bắt đầu sản xuất hàng loạt template NIL vào năm 2027 sau khi hoàn tất giai đoạn thử nghiệm với khách hàng. Không giống EUV vốn sử dụng ánh sáng cực tím để khắc mạch, NIL ép trực tiếp mẫu mạch lên wafer, giúp giảm chi phí sản xuất đáng kể. Phó Chủ tịch Nakanishi chia sẻ: “Nhiều khách hàng đang cân nhắc thay thế một số lớp mạch EUV bằng NIL để tối ưu chi phí. DNP đã nhận được nhiều yêu cầu hợp tác”.
Theo Semiconductor Engineering, NIL có thể giảm chi phí sản xuất chip xuống 30-40% so với EUV, đặc biệt phù hợp cho các chip không yêu cầu độ chính xác cực cao. DNP hiện đang thử nghiệm template NIL tại nhà máy Thượng Phúc (Saitama), phản hồi tích cực từ các đối tác như Canon và Tokyo Electron. So với đối thủ như ASML (gã khổng lồ EUV), NIL của DNP có lợi thế về chi phí nhưng vẫn cần thời gian để chứng minh độ ổn định trong sản xuất hàng loạt.
Ngoài photomask, DNP còn đầu tư vào TGV (Through-Glass Via) Glass Core Substrate, một vật liệu đóng gói tiên tiến cho chip AI và trung tâm dữ liệu. Theo Nikkei Asia, DNP sẽ khởi động dây chuyền thử nghiệm TGV tại nhà máy Kuki (Saitama) vào cuối năm 2025, mục tiêu sản xuất hàng loạt vào năm 2028. TGV sử dụng kính làm lõi thay vì nhựa, giúp tăng hiệu suất truyền tín hiệu và giảm tiêu thụ điện đến 20% so với tấm nền truyền thống.
DNP đang hợp tác với Shinko Electric Industries chuyên về đóng gói bán dẫn mà DNP đã đầu tư. Hai bên đang thảo luận để tối ưu hóa chuỗi cung ứng, tận dụng nhà máy Kuki để sản xuất TGV quy mô lớn. So với các đối thủ như Samsung Electro-Mechanics, TGV của DNP có lợi thế về độ chính xác và khả năng tích hợp với chip AI, nhưng việc triển khai sản xuất hàng loạt vẫn là bài toán khó. Theo EE Times Japan, việc chuyển đổi từ dây chuyền thử nghiệm sang sản xuất đại trà có thể mất 3-5 năm, đòi hỏi đầu tư lớn và rủi ro tài chính.
Photomask là “bản gốc” để in mạch lên wafer silicon, đóng vai trò then chốt trong sản xuất bán dẫn. DNP dự định tập trung vào hai hướng: sản xuất hàng loạt photomask EUV từ năm 2027 và tăng cường sản xuất photomask truyền thống cho các phân khúc khác. EUV là công nghệ tiên tiến, cần thiết để tạo ra các chip siêu nhỏ (2nm, 3nm) cho smartphone, trung tâm dữ liệu và AI. Theo EE Times Japan, DNP đã đạt thành tựu lớn khi thử nghiệm thành công mẫu mạch 2nm vào tháng 12/2024, đặt nền móng cho việc hợp tác với công ty Nhật Bản Rapidus, nhắm đến sản xuất chip 2nm vào 2027.
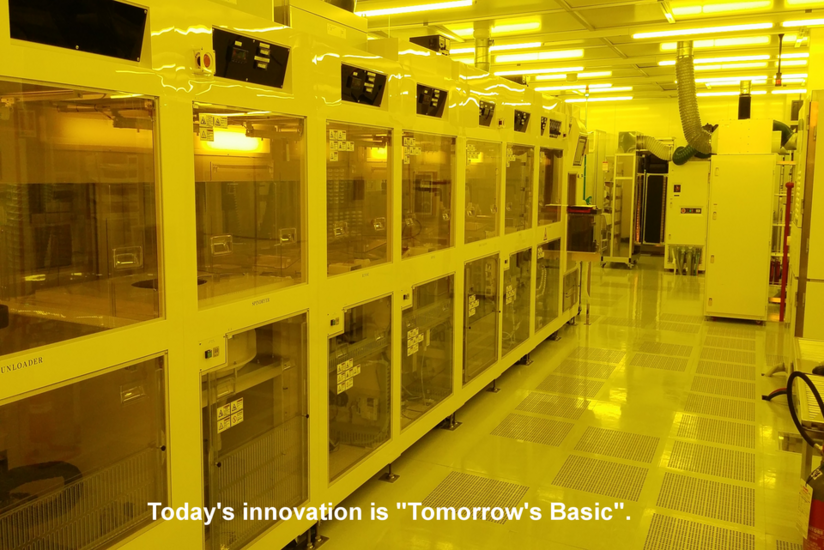
So sánh với đối thủ, DNP đang cạnh tranh khốc liệt với Toppan Photomasks, một công ty Nhật Bản khác. Theo Semiconductor Digest, Toppan hiện chiếm khoảng 15% thị phần photomask toàn cầu, trong khi DNP chiếm 10%. Tuy nhiên, khoản đầu tư 300 tỷ yên và hợp tác với Rapidus có thể giúp DNP vượt lên, đặc biệt ở phân khúc EUV.
Một điểm sáng trong kế hoạch DNP là phát triển Nanoimprint Lithography (NIL), công nghệ in nano được xem là giải pháp thay thế cho EUV. Theo Nikkei Asia, DNP sẽ bắt đầu sản xuất hàng loạt template NIL vào năm 2027 sau khi hoàn tất giai đoạn thử nghiệm với khách hàng. Không giống EUV vốn sử dụng ánh sáng cực tím để khắc mạch, NIL ép trực tiếp mẫu mạch lên wafer, giúp giảm chi phí sản xuất đáng kể. Phó Chủ tịch Nakanishi chia sẻ: “Nhiều khách hàng đang cân nhắc thay thế một số lớp mạch EUV bằng NIL để tối ưu chi phí. DNP đã nhận được nhiều yêu cầu hợp tác”.
Theo Semiconductor Engineering, NIL có thể giảm chi phí sản xuất chip xuống 30-40% so với EUV, đặc biệt phù hợp cho các chip không yêu cầu độ chính xác cực cao. DNP hiện đang thử nghiệm template NIL tại nhà máy Thượng Phúc (Saitama), phản hồi tích cực từ các đối tác như Canon và Tokyo Electron. So với đối thủ như ASML (gã khổng lồ EUV), NIL của DNP có lợi thế về chi phí nhưng vẫn cần thời gian để chứng minh độ ổn định trong sản xuất hàng loạt.
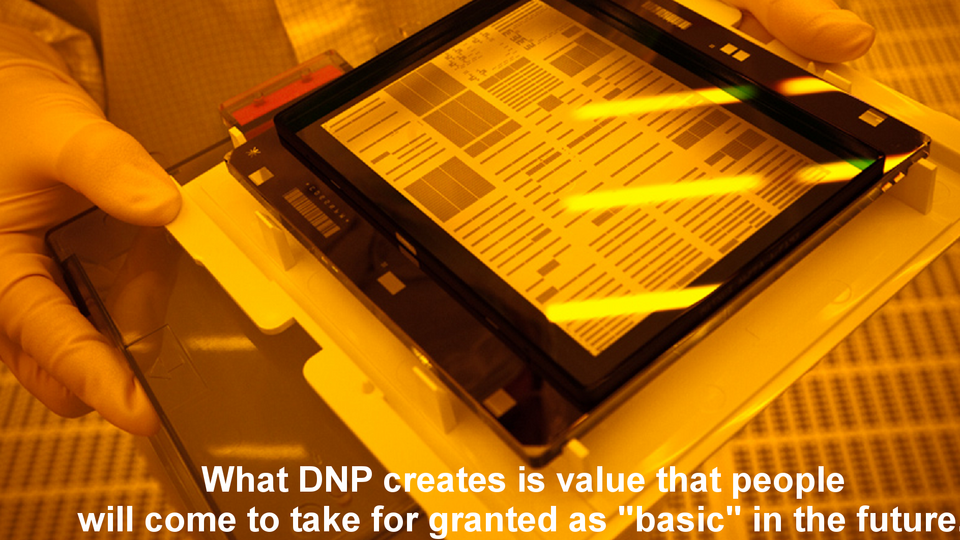
Ngoài photomask, DNP còn đầu tư vào TGV (Through-Glass Via) Glass Core Substrate, một vật liệu đóng gói tiên tiến cho chip AI và trung tâm dữ liệu. Theo Nikkei Asia, DNP sẽ khởi động dây chuyền thử nghiệm TGV tại nhà máy Kuki (Saitama) vào cuối năm 2025, mục tiêu sản xuất hàng loạt vào năm 2028. TGV sử dụng kính làm lõi thay vì nhựa, giúp tăng hiệu suất truyền tín hiệu và giảm tiêu thụ điện đến 20% so với tấm nền truyền thống.
DNP đang hợp tác với Shinko Electric Industries chuyên về đóng gói bán dẫn mà DNP đã đầu tư. Hai bên đang thảo luận để tối ưu hóa chuỗi cung ứng, tận dụng nhà máy Kuki để sản xuất TGV quy mô lớn. So với các đối thủ như Samsung Electro-Mechanics, TGV của DNP có lợi thế về độ chính xác và khả năng tích hợp với chip AI, nhưng việc triển khai sản xuất hàng loạt vẫn là bài toán khó. Theo EE Times Japan, việc chuyển đổi từ dây chuyền thử nghiệm sang sản xuất đại trà có thể mất 3-5 năm, đòi hỏi đầu tư lớn và rủi ro tài chính.